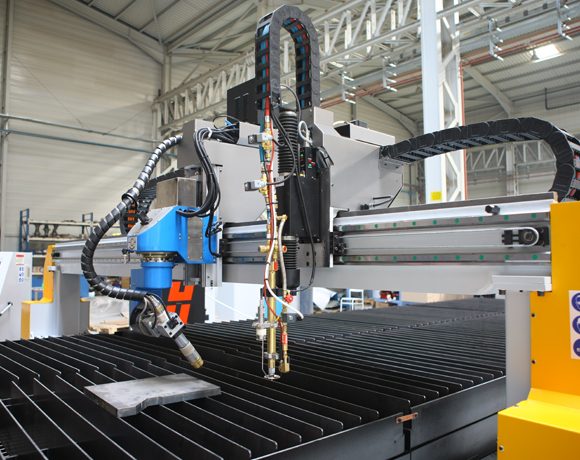
Cutting-Edge Precision: A Complete Guide to Industrial Plasma Cutting Machinery
In today’s fast-paced manufacturing industry, precision, efficiency, and adaptability are essential. Industrial plasma cutting machinery…
A Press Brake, sometimes known as a brake press, is a staple item in most sheet metal workshops. A brake press folding system is a dedicated piece of machinery used in sheet metal bending. At AFM our latest CNC press brakes are designed to meet diverse requirements, ranging from basic hydraulic press brake models to sophisticated servo-electric and hybrid options.
Whether you need swift and precise folding of brackets, user-friendly programming, or a focus on energy efficiency and environmental sustainability. Our press brakes come in a range of capacities, accommodating small compact machines to heavy-duty high-tonnage models. Our Ermaksan Machinery is made of high-strength monoblock st44 quality steel, ensuring record-level longevity. Ermaksan’s servo-electric and electro-hydraulic press brakes contribute to high-quality and efficient production all over the world.
A press brake is a machine tool commonly used in metalworking and fabrication processes to bend and shape sheet metal. It operates by applying force to a workpiece, typically positioned between a punch and a die. The punch exerts downward pressure on the material, forcing it into the predetermined shape defined by the die. Press brakes come in various sizes and configurations, ranging from manual and mechanical models to highly automated CNC (Computer Numerical Control) systems.
Press Brakes are essential in manufacturing processes where precise bending and forming of sheet metal components are required for the production of diverse products, such as automotive parts, appliances, and structural components. The versatility of press brakes makes them indispensable in various industries, allowing for the efficient and accurate creation of complex metal shapes with different angles and dimensions.
Press brakes are vital machines in the metalworking industry, used to bend sheet and plate material with high precision. The process begins by setting up the press brake with the appropriate punch (top tool) and die (bottom tool) based on the desired bend angle and material thickness. The sheet metal is then carefully positioned between the punch and die, often with the help of backgauges and automated controls for precise alignment.
The press brake applies downward force through hydraulic or mechanical systems to bend the metal to the predetermined angle. Advanced press brakes offer precise control over pressure, speed, and angle, ensuring consistent, high-quality bends. After the bending process, the pressure is released, and the component is inspected for accuracy.
Usually used in bottom bending where greater tonnage is used.
Acute angle dies (also known as air-bending dies) are used in air bending, these can also be used to produce acute, 90-degree and obtuse angles with varying depth depending how deeply the punch enters the die.
A combination punch and die set that bends two angles in one stroke to produce a Z shape.
Gooseneck dies (also known as return-flanging dies) are designed to allow for the clearance of already formed flanges.
Hemming dies are two-stage dies combining an acute angle die with a flattening tool.
In today’s fast-paced manufacturing industry, precision, efficiency, and adaptability are essential. Industrial plasma cutting machinery…
In the world of precision engineering and sheet metal fabrication, bending rolls are essential tools…
In an industry where precision, efficiency, and flexibility are critical to maintaining a competitive edge,…